在柔性印刷電路板(FPC)的應用中,折彎處的柔韌性與可靠性至關重要。合理運用 FPC 折彎機,并優化相關工藝,能夠有效提升 FPC 折彎處的這些關鍵性能。 優化折彎工藝參數
壓力調控:精確的壓力控制是提升 FPC 折彎處性能的基礎。壓力過大,會過度擠壓 FPC,導致內部線路受損,降低柔韌性與可靠性;壓力過小,則無法使 FPC 達到預期的折彎角度。需依據 FPC 的材質、厚度以及具體的折彎設計要求,通過反復試驗確定最佳壓力值。例如,對于厚度為 0.15mm 的聚酯(PET)材質 FPC,在進行 90° 折彎時,適宜的壓力可能在 8 - 12N 之間。通過壓力傳感器和反饋控制系統,可實時監測并調整壓力,確保每次折彎壓力的一致性。
速度優化:折彎速度對 FPC 折彎處的應力分布有顯著影響。過快的速度會使 FPC 瞬間承受較大應力,容易在折彎處產生裂紋,降低可靠性;過慢的速度雖能減少應力集中,但會影響生產效率。一般而言,適中的折彎速度在 5 - 10mm/s 較為合適。同時,可采用變速折彎的方式,在折彎起始和結束階段適當降低速度,以緩解應力突變,提升折彎處的柔韌性與可靠性。
選擇合適的模具
模具材質:模具材質直接關系到 FPC 的折彎質量。應選用硬度高、耐磨性好且表面光滑的模具材質,如合金鋼或鎢鋼。這些材質能有效減少模具與 FPC 表面的摩擦,降低 FPC 表面劃傷的風險,從而提高折彎處的可靠性。同時,良好的耐磨性可保證模具在長時間使用過程中保持穩定的形狀和尺寸精度,確保 FPC 折彎角度的一致性。
模具形狀與尺寸:模具的形狀和尺寸需與 FPC 的折彎要求精確匹配。例如,對于半徑較小的弧形折彎,應采用具有相應曲率半徑的模具,以保證 FPC 在折彎過程中受力均勻,避免局部應力集中。此外,模具的尺寸精度要控制在較高水平,如模具的公差范圍應控制在 ±0.05mm 以內,確保 FPC 折彎處的形狀精度和穩定性。
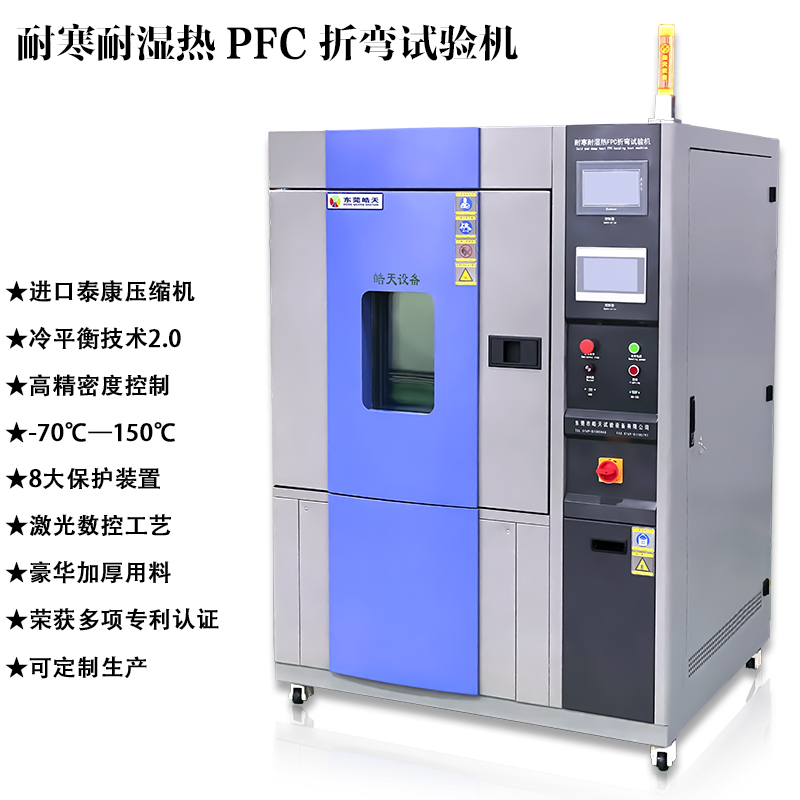
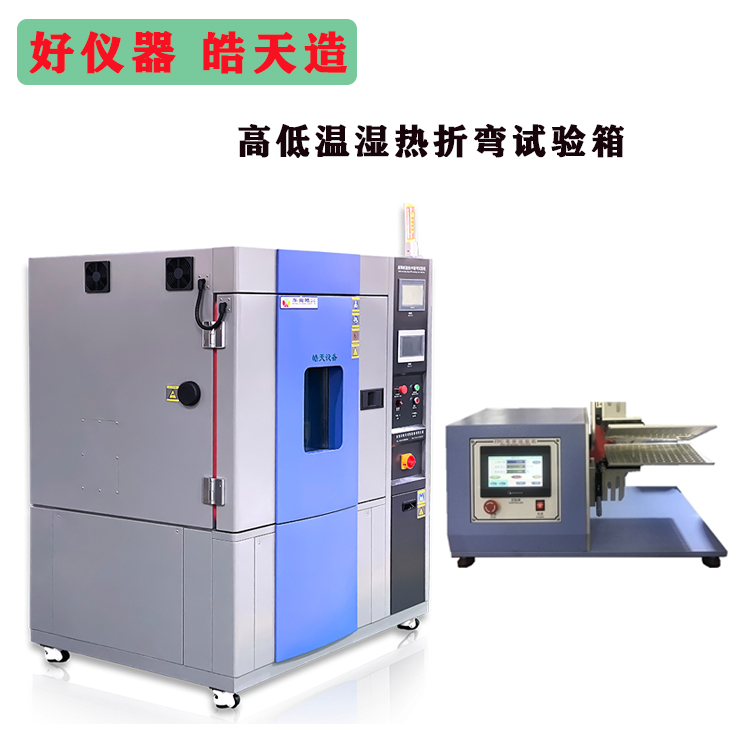
折彎前預處理與折彎后處理
預處理:在折彎前,對 FPC 進行適當的預熱處理,可有效降低材料的脆性,提高其柔韌性。例如,將 FPC 在 60 - 80℃的烘箱中預熱 10 - 15 分鐘,使材料分子鏈的活動能力增強,在折彎過程中能更好地適應變形,減少裂紋的產生。此外,對 FPC 表面進行清潔處理,去除灰塵、油污等雜質,可避免這些雜質在折彎過程中導致應力集中,提高折彎處的可靠性。
后處理:折彎后,對 FPC 折彎處進行應力釋放處理。可采用低溫退火的方法,將 FPC 在一定溫度(如 50 - 70℃)下保持 30 - 60 分鐘,使折彎處的內部應力得到緩解,從而提高柔韌性和可靠性。同時,在折彎處涂覆一層保護膠,如 UV 固化膠或三防漆,可增強折彎處的機械性能和耐環境性能,進一步提升其可靠性。
通過優化 FPC 折彎機的工藝參數、選擇合適的模具以及做好折彎前后的處理工作,能夠顯著提高 FPC 折彎處的柔韌性與可靠性,滿足日益嚴苛的電子設備制造需求。